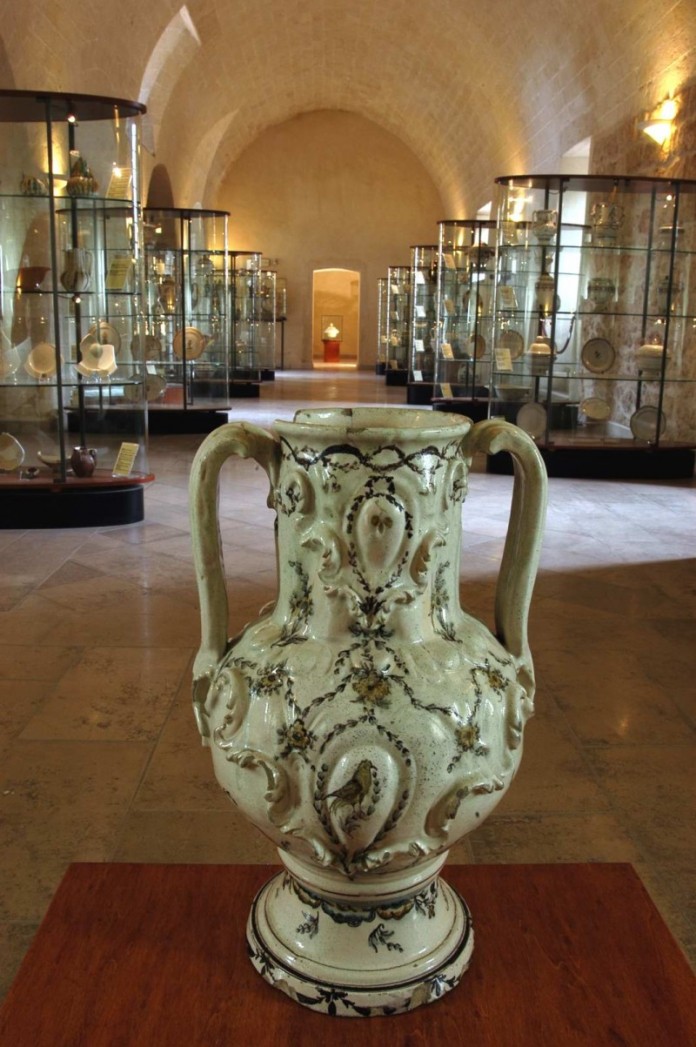
L’essiccamento
Una volta che il manufatto risulta essere completo in ogni sua parte è pronto per l’essiccamento. L’operazione dell’essiccamento richiede tempo e una serie di conoscenze che riguardano la temperatura esterna e le correnti d’aria. Infatti, a seconda delle stagioni e delle condizioni atmosferiche, i manufatti vengono sistemati gli uni accanto agli altri pezzi della serie, per terra in bottega oppure nel piazzale esterno in una zona fresca e ombreggiata.
I pezzi sono molto delicati e temono le correnti d’aria e i bruschi cambiamenti di temperatura. Man mano che passano le ore il pezzo tende ad indurirsi acquisendo maggiore resistenza. Sul tempo che occorre per essiccare ed acquisire resistenza influiscono dimensioni, forma e spessore del manufatto. Per alcuni tipi, infatti, la fase dell’essiccamento richiede maggior cura e attenzione soprattutto per quel vasellame dalla bocca larga di cui bisogna evitare la deformazione dei bordi. Per questo motivo si mettono bocca contro bocca per qualche giorno, quindi la posizione è capovolta per far raggiungere lo stesso grado di essiccamento sia ai manufatti posti sopra che a quelli posti sotto. Infine, vengono posizionati con la bocca all’ingiù per eliminare quell’umidità che si forma all’interno del pezzo.
Altri manufatti più elaborati necessitano di tempi lunghi e di numerose attenzioni durante questa fase affinché l’acqua dell’impasto evapori gradualmente. Fanno parte di questa categoria la “burraccia” che ha la forma di un anello con all’interno due condotti concentrici e non comunicanti e che richiede una quindicina di giorni di permanenza in ambiente umido, lontano da fonti di calore e da correnti d’aria, altri quindici giorni in ambiente asciutto e infine un periodo di tempo vicino alla fornace in attività.
Rientrano anche i “pumi de’ fiuri”, ovvero boccioli di fiore stilizzati che vengono apposti agli angoli dei balconi come elementi decorativi ma anche come simboli di abbondanza e prosperità, e i “fironi” ovvero i salvadanai. In queste forme, apparentemente chiuse, è indispensabile avere un’apertura che consente, sia durante l’essiccamento ma soprattutto durante la cottura, di far uscire i vapori acquei e i gas derivanti dalla decomposizione del calcare che si formano all’interno del manufatto.
Nei “pumi de’ fiuri” l’apertura è rappresentata dal foro praticato sotto la base mentre nel salvadanaio dalla feritoia sulla spalla. Dopo la fase dell’essiccamento i manufatti appartenenti alla “robba rustica” vengono portati alla fornace per essere cotti mentre quelli che fanno parte della “robba gialla” o “robba bianca” vengono prima ricoperti con l’ingobbio poi con l’invetriatura acquisendo impermeabilità e lucentezza.
La preparazione dei rivestimenti al mulino
Prima di passare alla fase dell’ingobbiatura e dell’invetriatura è necessario preparare i rivestimenti vetrosi e i coloranti per ricoprire sia la “robba gialla” che la “robba bianca”. Essi, un tempo, venivano preparati mediante la macinazione a umido servendosi di mulini. Prima di passare alla macinazione, il piombo, con cui venivano realizzati i rivestimenti, doveva essere calcinato, ovvero subire una fusione in atmosfera ossidante per trasformarsi in ossido di piombo e ciò avveniva all’interno di fornetti a riverbero, che generalmente era localizzato all’interno della bottega, costruito dallo stesso vasaio addossandolo a una delle pareti del locale dove si trova la fornace.
Il fornetto aveva piccole dimensioni ed era costituito da due aperture affiancate di cui una soltanto era dotata di sportello. Il forno era chiuso, nella parte superiore, da una volta di tubuli fittili cavi. I gas di combustione salgono spontaneamente verso l’altro e fuoriescono dalla bottega mediante un’apertura sul tetto che funge da camino per la fornace. All’interno del fornetto si trovano due vaschette rettangolari che un tempo erano costituite da mattoni, oggi, invece, sono in metallo. Vengono posizionate l’una accanto all’altra, separate da un muretto divisorio.
Il piombo da calcinare viene posizionato sulla vaschetta del lato destro corrispondente all’apertura senza sportello, mentre il fuoco viene acceso nella vaschetta di sinistra dove lo sportello viene tenuto semichiuso per risparmiare calore tra un carico e l’altro di combustibile. Il piombo viene continuamente rimescolato utilizzando un’asta metallica lunga due metri la cui estremità è curvata e viene definita “cranfodda”, che viene sostituita perché tende a surriscaldarsi rimanendo per tante ore vicino al fuoco. A intervalli regolari getta, nella vaschetta affianco, legna, gusci di mandorle, sansa per rinvigorire la fiamma. I gas prodotti raggiungono la volta del fornetto e non avendo altra via d’uscita invertono il loro percorso fuoriuscendo dall’apertura corrispondente alla vaschetta che contiene il piombo.
Il metallo riceve il calore riverberato e si fonde in maniera graduale poi diventa liquido e infine si rassoda in una polvere granulosa più o meno fine che tende a rifondersi ma l’operaio rimescolando continuamente il piombo impedisce che si fonda e lo mantiene in forma granulosa. Essa viene definita “litargirio” o “piombo calcinato” o “piombo giallo” la cui qualità dipende dalle condizioni in cui avviene la fusione e dalla qualità del materiale usato che talvolta è piombo in pani, ma molto spesso sono scarti di tubature idrauliche o munizioni da caccia o ancora materiale di recupero proveniente da navi in demolizione.
Per controllare il grado di calcinazione, l’operaio provvede ad estrarre un pizzico di polvere e la strofina su un vaso di terracotta, se la striscia ha un colore scuro vuol dire che l’ossidazione è ancora in atto, se invece, è giallo, indica la conclusione del ciclo. Questa è una lunga operazione che costringe l’operaio a rimanere vicino a una fonte di calore per quasi quattro ore. Egli deve avere molta esperienza nel dosaggio del fuoco e deve prestare molta attenzione. Una volta terminata la calcinazione il piombo viene tolto dalla vaschetta e quando si raffredda viene setacciato, dopodichè è pronto per la macinazione insieme con la silice.
Varie tipologie di mulino
Il mulino, di tipologie differenti, costituisce uno strumento indispensabile nella bottega del figulo, poiché serve ad amalgamare gli ingredienti del rivestimento ovvero sabbia silicea e piombo calcinato al fine di preparare i coloranti da aggiungere alla miscela per ottenere tonalità cromatiche desiderate. La qualità del risultato è determinata sia dalla tecnica che dalla durata della macinazione. Il mulino più semplice è quello azionato a mano, detto più comunemente macina, costituito da due pietre di tenero tufo calcareo che sfregano l’una contro l’altra e al centro si trova un profondo incavo rotondo dal diametro variabile da 40 a 80 cm circa che veniva riempito da ciottoli di mare e uniti a un impasto sabbioso formavano uno strato resistente che col passar del tempo veniva levigato dall’azione della pietra – mulino.
All’interno della macina venivano poste le sostanze da macinare insieme con la giusta quantità d’acqua che la pietra – mulino con il suo movimento continuo polverizzava e amalgamava in una miscela densa e omogenea. L’operazione era molto lunga e veniva curata da vasai anziani o da apprendisti e qualche volta dalle donne della famiglia. Era questo l’unico caso in cui le donne lavoravano. Per rendere più veloce il lavoro alcuni figuli avevano inventato dei marchingegni che consentivano di azionare la macina mediante l’alzarsi o l’abbassarsi di una leva, meccanismi rudimentali di cui non è rimasta traccia.
In alcune botteghe, dove la produzione era fiorente, la macina veniva sostituita dal mulino a trazione animale che è rimasto in uso fino all’inizio del ‘900, come racconta Ninina Cuomo Di Caprio nella sua opera citata: “Consisteva in una grossa ruota orizzontale dentata messa in moto da un mulo e collegata mediante vari congegni a pesanti pietre che agendo da macine schiacciavano gli ingredienti posti dentro larghe vasche circolari in muratura. Costruito all’interno della bottega, il mulino occupava una stanza che doveva essere sufficientemente larga sia per contenere le vasche sia per permettere al mulo di girare loro attorno. […] la robusta ruota orizzontale dentata aveva un asse verticale imperniato in apposite sedi fissate in basso nel pavimento e in alto ad una trave murata a due pareti opposte della stanza.
All’asse era collegata una stanga alla cui estremità era aggiogato il mulo: questo tramite la stanga trasmetteva il movimento all’asse che a sua volta faceva girare la ruota. I denti della ruota penetravano tra sbarra e sbarra di grosse gabbie circolari in ferro chiamate macennili collocate ognuna al centro di una vasca, e le costringevano a girare su se stesse. Mediante tiranti e catene a ogni macennila erano agganciate pesanti pietre tonde chiamate minatori che trascinate nel continuo movimento agivano da macine, schiacciando gli ingredienti e amalgamandoli insieme all’acqua aggiunta dentro le vasche per diminuire l’attrito e facilitare lo scorrimento .”
Le vasche erano generalmente tre e venivano costruite sotto la ruota dentata alla stessa distanza tra loro. Ciascuna di esse aveva una capacità di 50 kg di prodotto finito. Talvolta ce ne potevano essere quattro di cui tre riservate alla macinazione di piombo e silice e quella più piccola, invece, alla macinazione dei coloranti. La ruota dentata metteva in funzione tutte e tre le vasche contemporaneamente ma quando si voleva risparmiare le forze del mulo si spostavano i “macenili” e la lavorazione veniva ridotta a due vasche.
Al collo del mulo, cieco o bendato, si legava un collare dotato di campanelli il cui rumore lo teneva desto. Lo scampanellio era indice di attività mentre quando si sentiva silenzio significava che il mulo si era fermato e allora l’apprendista o il vasaio pungolava l’animale con il bastone obbligandolo a proseguire il lavoro. L’intera operazione di macinazione durava quattro giorni. All’inizio non vi erano soste per impedire al materiale di attaccarsi sul fondo delle vasche poi il vasaio ogni quattro o cinque ore fermava il mulo per controllare l’andamento del lavoro e per staccare la crosta formatasi lungo il bordo interno della vasca.
Un altro tipo di mulino è quello a tamburo che risulta essere più efficace rispetto a quello a giogo perché consente di amalgamare gli ingredienti del rivestimento in meno tempo, in dodici ore circa, un quarto del tempo che veniva impiegato con il mulino a trazione animale, per la cui descrizione ci affidiamo ancora al racconto di Ninina Cuomo Di Caprio: “Composto da un grosso tamburo metallico mantenuto in costante rotazione da un motore, esso contiene all’interno una massa di ciottoli rotondi che battendo continuamente tra loro schiacciano ed amalgamano gli ingredienti del rivestimento. L’interno del tamburo è foderato con blocchetti di granito dalla grandezza di un pugno, attaccati mediante cemento dal lato a contatto con la parte metallica del tamburo, mentre le giunture tra blocchetto e blocchetto non sono cementate ad evitare che venendo a contatto con i ciottoli il cemento subisca un’azione abrasiva, ossia una smerigliatura, e si mescoli agli ingredienti del rivestimento alterandone la composizione.”
Essendo composti da quarzo ovvero da silice, i ciottoli che fungono da macine non arrecano danni pur frantumandosi e consumandosi durante la macinazione.
La macinazione dei coloranti
La macinazione dei coloranti avviene separatamente rispetto a quella che consente di amalgamare gli ingredienti del rivestimento anche per evitare contaminazioni. Il ventaglio dei colori a disposizione del vasaio è generalmente ridotto e riguarda alcuni ossidi metallici: Gli ossidi di ferro provocano colorazioni che variano dal giallo miele al giallo – bruno; aumentandone la percentuale e applicando il rivestimento in strato denso si possono ottenere tonalità rossastre con tendenza al rosso – bruno. Gli ossidi di rame danno il verde in gradazioni variabili. L’ossido di manganese dà il colore paonazzo e un’ampia gamma dei bruni dal giallo bruno al nero.
L’antimonio dà il giallo canarino. Gli ossidi di ferro più largamente utilizzati sono chiamati “farruma” e “firrucina”. La “farruma” è costituita da scarti di lavorazione del fabbro che avendo già subito l’azione del fuoco non era necessario cuocerli nuovamente nella fornace e potevano essere messi direttamente nel mulino. Ha una maggiore potenza colorante rispetto alla “firrucina” e ciò consentiva di usarne una quantità minore pur ottenendo la stessa intensità di tinta.
La “firrucina” deriva dalla calcinazione di scatolame metallico che può essere costituito da lattine da conserva in banda stagnata o da qualsiasi altro tipo di scatolame in lamiera sottile. Dopo aver schiacciato i barattoli con il martello per ridurne il volume il vasaio li pone nella fornace in fondo alla camera di combustione dove le temperature sono più elevate affinché subiscano una lunga cottura che consente poi di facilitarne la macinazione. Tolti dalla fornace vengono lavati in acqua fredda per togliere eventuali residui di combustione dopodichè vengono posti nel mulino per la macinazione allo scopo di ottenere una miscela granulosa.
Dagli scarti di lavorazione veniva ricavato l’ossido di rame che dà la colorazione verde. I resti della lavorazione del rame, ovvero le scaglie che si staccavano dal metallo arroventato quando il fabbro vi batteva sopra il martello, venivano regalati ai vasai che li macinavano direttamente. Un altro ossido metallico usato dai figuli è quello ricavato dal manganese che dà un colore paonazzo oppure marrone bruciato e nero. È un minerale che proviene solitamente dalla Calabria che viene ridotto in grossi frammenti e poi messo nella fornace e lasciato cuocere coperto dalla brace ardente per più cotture successive.
L’ossido di manganese ha un duplice utilizzo: mescolato al rivestimento piombifero provoca una colorazione marrone scuro mentre usato come colore per la decorazione serve per disegnare sul manufatto gli ornati a linea o a macchia.